The AI and Automation Paradox in Manufacturing: Replacing Humans, Yet Creating New Jobs
As artificial intelligence (AI) and robotics become increasingly embedded in our daily lives, a natural question arises: will these technologies assist us or pose challenges? Rapidly evolving technologies are automating tasks once performed by humans, fundamentally altering traditional work and living models.
“I see AI not merely as lines of code, but as a mechanism with an electromechanical “body” – something tangible that can manipulate objects in time and space, considering production needs,” says Professor Vidas Raudonis from Kaunas University of Technology (KTU), a member of the SustAInLivWork project.
He asserts that AI and robotics in manufacturing do not simply replace humans, but rather expand their capabilities. By automating repetitive tasks, these technologies reduce worker fatigue and the likelihood of errors, while also taking over hazardous tasks, significantly minimising the risk of accidents.
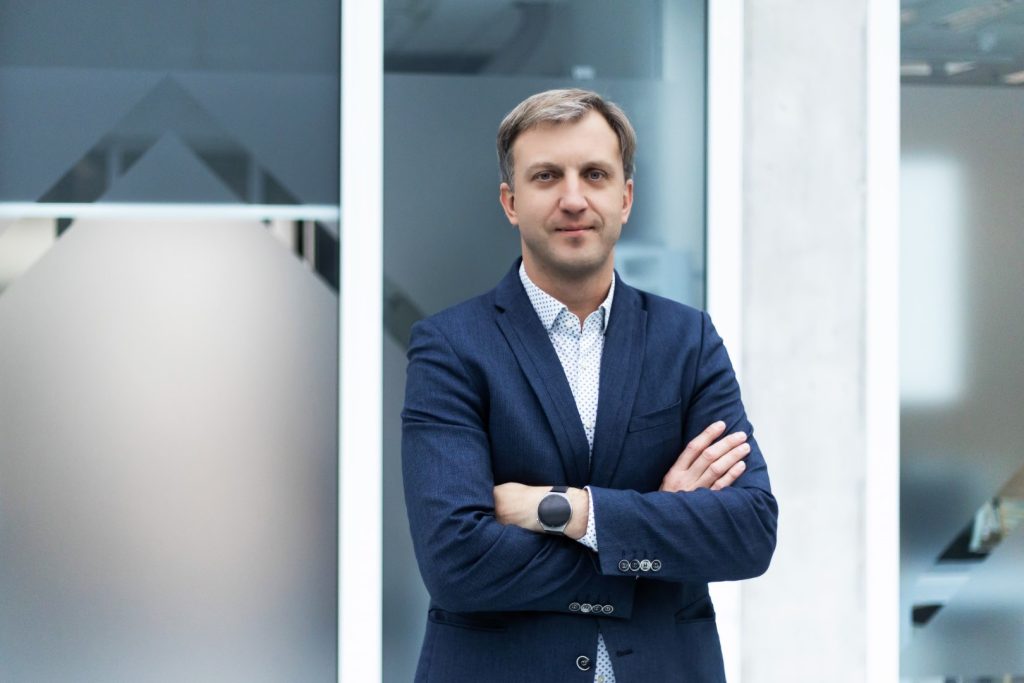
Despite widespread concerns that AI may replace humans, these technologies, in fact, allow for faster, more efficient, and safer work. A future where factories operate without direct human intervention, and complex manufacturing processes are modelled in virtual spaces, is already becoming a reality.
Digital Twins
According to Prof. Dr Raudonis, AI, including machine learning, has become integral to the creation of digital twins. A digital twin is a virtual replica of a real physical object or process, reflecting all the physical laws that govern the actual object or process.
“Imagine creating a digital replica of a product without physically moving a single screw in the real world,” he explains.
Utilising digital twins in manufacturing allows for the simulation of an entire production line in a virtual environment, where all stages occur just as they would in the real world – from raw material supply to the final product’s packaging.
Prof. Dr Raudonis notes that this increases manufacturing flexibility, as it allows potential disruptions in the production process to be identified and the impact on efficiency and productivity to be evaluated.
“A digital replica of the manufacturing process allows new employees to be trained to operate potentially hazardous equipment without physically touching it. Virtual reality (VR) technologies and haptic devices, which simulate physical contact with virtual objects, are used to train new workers,” he adds.
The KTU professor acknowledges that creating a fully functional digital twin of a manufacturing process is complex. However, global companies such as Siemens and Nvidia offer smart solutions for the industrial sector. For instance, the Industrial Metaverse product replicates elements of the physical world – real devices, factories, buildings, cities, and other infrastructure – helping clients create digital replicas.
The Revolution of Dark Factories
Prof. Dr Raudonis asserts that AI technologies enable the development of so-called “dark factories” – fully automated factories that operate without human workers and therefore do not require lighting.
“Since there are no workers, there is no need to illuminate the factory premises. Such factories operate efficiently and productively, unaffected by holidays, strikes, or other human factors,” he states.
The KTU researcher reports that fully automated factories are already in operation globally, controlled by companies such as Lego. Interestingly, in these factories, turning the lights on triggers an alarm. “This raises the question: what is the role of humans in such an environment? This challenge extends beyond industry and affects the broader socio-economic fabric of society,” he observes.
Prof. Dr Raudonis predicts, automation will continue to impact numerous jobs in the future, particularly those involving repetitive tasks, such as pick-and-place operations.
“Humans must embrace the opportunities presented by AI technologies. These technologies free individuals from routine, often hazardous tasks, enabling them to pursue new activities that require more complex cognitive skills,” he explains.
High Skilled Workers Are Safe from Redundancy
The KTU researcher highlights that the integration of AI and robotics in Germany’s manufacturing sector is on the rise; however, this does not imply a decreasing demand for workers. On the contrary, automation is occurring due to a shortage of available labour. Although automated processes require highly skilled specialists, their scarcity hampers the rapid deployment of AI and robotics, meaning that manufacturing still partially relies on physical labour.
“In Germany, over half of workers view industrial robots positively, as they assist with difficult tasks and enable older employees to remain in the workforce for longer. Germans have a culturally favourable attitude towards the implementation of technology, recognising that automation enhances safety and reduces the number of dangerous tasks. Nonetheless, a third of manufacturing companies report a shortage of specialists capable of working with new technologies,” says Prof. Dr Raudonis.
The German government promotes employee upskilling by offering a dual learning and practical leave programme, alongside providing financial support to employers under the Qualification Opportunities Act. This initiative enables employees to learn and acquire new skills.
Private companies are also investing in the development of their employees, and as Prof. Dr Raudonis notes, high-skilled workers are not at risk of redundancy.
“While it was anticipated that AI, much like automation, would liberate people from everyday tasks and allow for greater creative expression, the reality often different. Current AI algorithms successfully automate cognitive tasks, such as writing texts and generating images, but they still struggle with everyday physical tasks, such as washing dishes or tying shoelaces,” says the SustAInLivWork project member.
He suggests that large companies in the cognitive technology sector will reduce their workforce as automation accelerates. However, until we possess robots capable of performing all physical tasks, the demand for human labour remains crucial. As a result, many will need to acquire new skills to successfully adapt to this evolving reality.